The Advantages of HDPE Rock Bag Filter Units
When comparing High-Density Polyethylene (HDPE) with general Polyethylene (PE) for sensitive environments such as marine applications, several advantages of HDPE become apparent:
Superior Strength and Durability: HDPE has a higher tensile strength and greater resistance to environmental factors such as UV radiation, temperature fluctuations, and abrasion compared to standard PE. This makes HDPE more durable and longer-lasting in harsh environments.
Enhanced UV Resistance: Rock Bag Filter Units contains Carbon Black, which provide superior UV resistance. This ensures that the netting maintains its strength and integrity over extended periods of exposure to sunlight, crucial for above surface and marine applications where UV degradation is a concern.
Reduced Environmental Impact: Rock Bag Filter Units HDPE netting is less prone to breaking down into microplastics compared to standard PE, especially recycled types. This reduces the risk of environmental pollution and harm to marine ecosystems, aligning with sustainability goals and environmental regulations.
Improved Performance in Marine Conditions: The molecular structure of HDPE, characterized by linear chains with minimal branching, provides better resistance to thermal degradation and chemical exposure commonly encountered in marine environments. This results in enhanced performance and reliability of HDPE marine netting under challenging marine conditions.
Compliance with Safety Standards: Rock Bag Filter Units HDPE netting is manufactured to exceed industry standards ensuring compliance with safety regulations and certifications. This provides assurance of product quality and reliability for the vast range of applications where safety is paramount.
Overall, the advantages of HDPE over standard PE netting includes superior strength, durability, UV resistance, environmental sustainability, performance in marine conditions, customization options, and compliance with safety standards. These factors make HDPE an excellent choice for applications where reliability and longevity are essential.
Microplastics
Microplastic release refers to the shedding or fragmentation of plastic particles smaller than 5 millimeters in size. These particles can originate from various sources, including plastic products and materials exposed to environmental factors such as UV radiation, mechanical stress, and degradation over time.
In the context of comparing HDPE (High-Density Polyethylene) and PE (Polyethylene) materials, the potential for microplastic release can vary depending on several factors:
Material Composition: HDPE is generally considered to be less prone to breaking down into microplastics compared to standard PE, particularly recycled PE. This is due to HDPE’s higher molecular weight and greater resistance to environmental degradation.
Additives and Stabilizers: Our HDPE Rock Bag Filter Units use Black as the UV blocker, which provide UV resistance and help prevent degradation. These additives can contribute to the material’s durability and reduce the likelihood of microplastic release compared to PE without such additives.
Environmental Conditions: Exposure to environmental factors such as UV radiation, temperature fluctuations, and mechanical stress can accelerate the degradation of PE materials, potentially leading to microplastic release. HDPE’s superior resistance to these factors mitigates the risk of microplastic generation.
Product Design and Use: The design and intended use of HDPE and PE products can also influence the likelihood of microplastic release. For example, products subjected to high levels of abrasion or mechanical stress are more likely to shed microplastic particles over time.
While both HDPE and PE materials can contribute to microplastic pollution under certain conditions, HDPE is generally considered to be more resistant to degradation and less prone to microplastic release compared to standard PE or recycled PE.
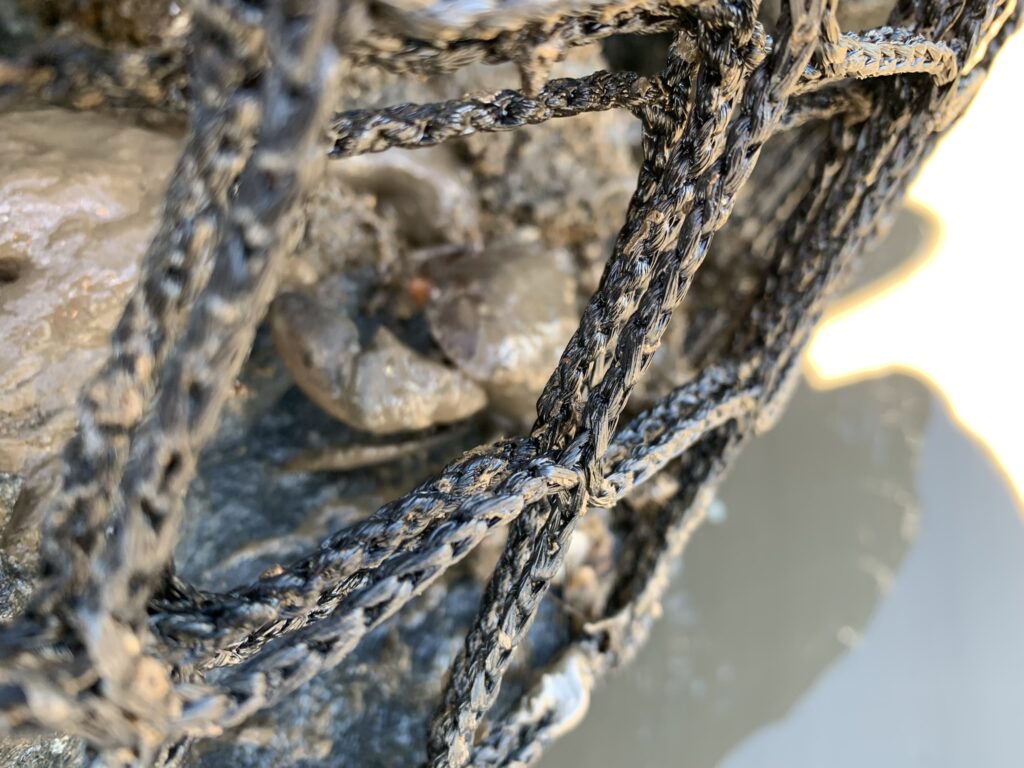
What are the disadvantages of recycled PE?
Recycled PE may have lower mechanical properties, such as tensile strength and impact resistance, compared to virgin PE. In harsh marine environments with factors like UV radiation, saltwater exposure, and wave action, reduced durability can lead to quicker degradation and shorter lifespan of products made from recycled PE.
Susceptibility to Environmental Degradation: The recycling process can degrade the molecular structure of PE, making recycled PE more susceptible to environmental factors like UV radiation, temperature fluctuations, and chemical exposure. This can accelerate degradation and compromise the performance of recycled PE materials in marine applications.
Potential for Microplastic Release: Due to its lower durability and increased susceptibility to degradation, recycled PE products in marine environments may shed microplastic particles over time. These microplastics can contribute to environmental pollution and harm marine ecosystems, posing risks to aquatic life and ecosystems.
Contaminants: Recycled PE may contain contaminants such as dirt, debris, or residues from previous uses, which can compromise the material’s performance and suitability for marine applications. Contaminants can also contribute to environmental pollution and degradation if released into the marine environment.
Limited Performance: In marine applications where reliability, longevity, and performance are critical, recycled PE may not meet the necessary standards or requirements. Products made from recycled PE may be more prone to failure, corrosion, or deterioration compared to those made from virgin PE or HDPE, impacting their effectiveness and safety in marine environments.
Regulatory Compliance: Depending on the specific marine application and regulatory requirements, there may be standards or specifications governing the use of materials like recycled PE. Meeting these regulatory requirements and ensuring compliance can be challenging for manufacturers or suppliers using recycled PE in marine products, potentially limiting their market access or applicability.
Overall, while recycled PE offers environmental benefits such as waste reduction and resource conservation, its disadvantages in sensitive environments and marine applications include reduced durability, susceptibility to environmental degradation, potential for microplastic release, presence of contaminants, limited performance, and challenges with regulatory compliance.